3. Plane Stress State
The plane stress state (also known as biaxial stress state or two-dimensional stress state) occurs when there is a two-dimensional load.
This happens in an element that is cut from a thin plate and is loaded only within its plane:
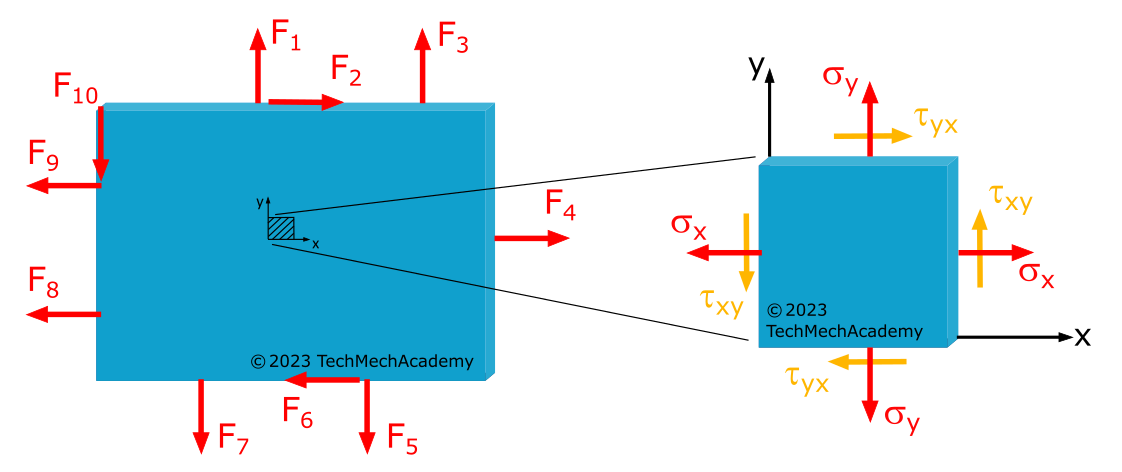
Figure 1.3.1 shows a disc loaded in the \(x, y\)-plane, with no load in the \(z\)-direction. Therefore, we have a stress-free surface with
Of course, a loaded \(x, z\)-plane could also exist with an unloaded \(y\)-axis, or a loaded \(y, z\)-plane with an unloaded \(z\)-axis. The orientation of the coordinate system in the respective plane does not matter. All of these cases meet one of the conditions for the presence of a plane stress state: a planar load with a stress-free surface.
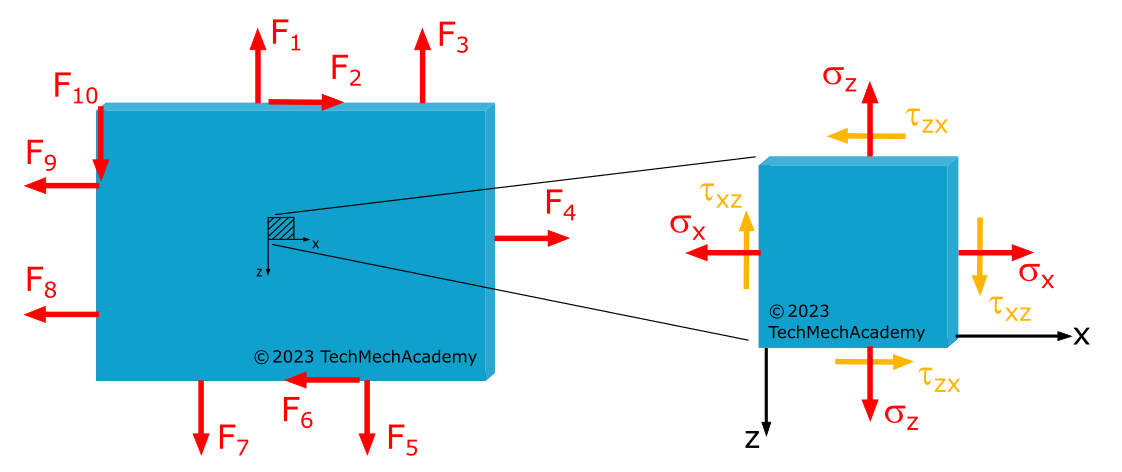
Another condition for the plane stress state is that the thickness of the component is small relative to its length dimensions, meaning there is a thin wall. Only in this case can we assume that the stresses \(\sigma_x, \sigma_y\), and \(\tau_{xy} = \tau_{yx}\) are uniformly distributed over the entire thickness of the disc.
Not entirely clear about the difference between \(\tau_{xy}\) and \(\tau_{yx}\) or \(\tau_{xz}\) and \(\tau_{zx}\)? Refer to the Index of (Shear) Stresses.
Not entirely clear why \(\tau_{xy} = \tau_{yx}\) or \(\tau_{xz} = \tau_{zx}\)? Refer to the Associated Shear Stresses.
Not entirely clear why the directions of shear stresses differ in Figures 1.3.1 and 1.3.2? Refer to the Determination of Sign for Normal and Shear Stresses.
3.1 Normal and Shear Stresses at Any Angle - Coordinate Transformation
What interests us are not only the normal and shear stresses \(\sigma_x, \sigma_y\), and \(\tau_{xy} = \tau_{yx}\) (according to Figure 1.3.1) or \(\sigma_x, \sigma_z\), and \(\tau_{xz} = \tau_{zx}\) (according to Figure 1.3.2) parallel to the coordinate axes, but rather the stresses at any angle \(\varphi\).
Ultimately, it's important to know at what angle \(\varphi\) the largest or smallest stresses act at the examined point of the component and how large they are. This knowledge is essential, for example, in choosing the angles for necessary welds to minimize the loads on these welds.
To derive the coordinate transformation for the plane stress state, we can do this for two different coordinate systems: once for a Cartesian coordinate system with a positive x-axis to the right and a positive y-axis upward, as shown in Figure 1.3.1, and once for a Cartesian coordinate system with a positive x-axis to the right and a positive z-axis downward, as shown in Figure 1.3.2.
We need to make this distinction because the direction of shear stresses in the plane depends on the choice of the coordinate system. This is due to the defined sign determination for normal and shear stresses. In practice, it is sufficient to know the derivation for a preferred coordinate system and be able to calculate its coordinate transformation. However, since both systems are frequently used, both derivations are shown at this point.
3.1.1 Coordinate Transformation for a Cartesian Coordinate System with Positive X-Axis to the Right and Positive Y-Axis Upward
To define stresses at any angle, just as in the one-axial stress state, we introduce a coordinate system rotated by the (cutting) angle \(\varphi\). We call the rotated \(x\)-axis \(\xi\) (Xi) and the rotated \(y\)-axis \(\eta\) (Eta).
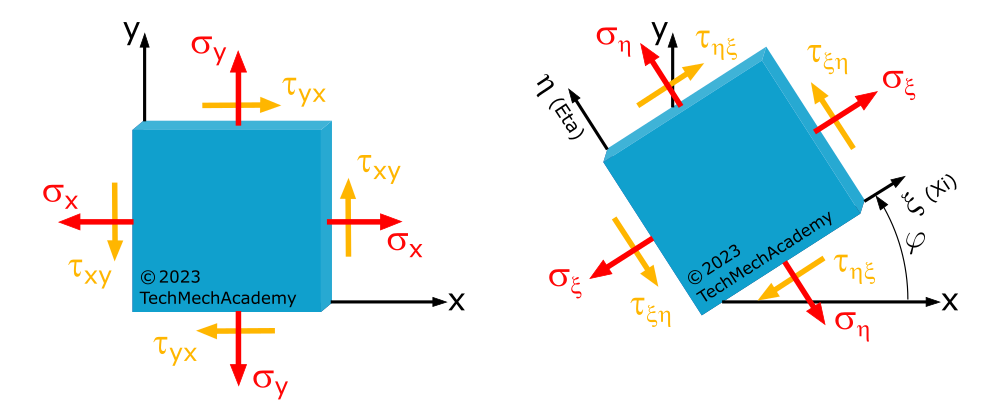
We obtain the normal stresses \(\sigma_{\xi}\), \(\sigma_{\eta}\), and the shear stresses \(\tau_{\xi\eta} = \tau_{\eta\xi}\).
The cutting angle \(\varphi\) is counted positively counterclockwise in the \(x, y\)-coordinate system at the examined element (see Right-Hand Rule in the Cartesian coordinate system + Right-Hand Thumb Rule for determining the positive rotation direction).
To mathematically link the two coordinate systems from Figure 1.3.3, we cut the area element in the \(x, y\)-coordinate system at the angle \(\varphi\) and place the stresses on the surfaces:
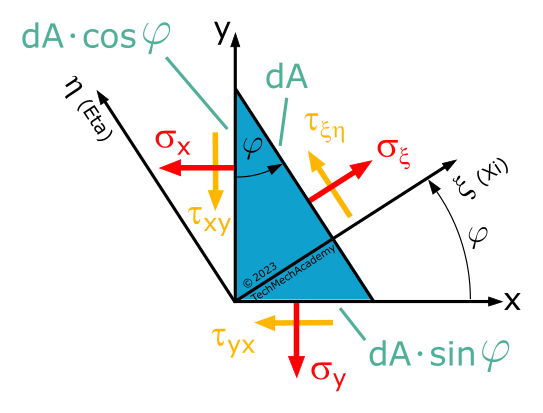
We establish equilibrium equations for both the \(\xi\)- and \(\eta\)-directions.
Note:
Since equilibrium statements apply only to forces, we need to multiply the stresses by the area elements on which they act!
We can factor out and eliminate \(\mathrm{d}A\) from both equations (2) and (3).
With \(\tau_{yx} = \tau_{xy}\), we then get:
In summary, we have determined the stresses occurring at any angle as follows:
Now, we need a formula for the normal stress \(\sigma_{\eta}\). This normal stress acts at an angle of 90° (or \(\frac{\pi}{2}\)) to the normal stress \(\sigma_{\xi}\).
So, we can use the derived formula for the normal stress \(\sigma_{\xi}\) and replace \(\sigma_{\xi}\) with \(\sigma_{\eta}\) and \(\varphi\) with \(\varphi + \frac{\pi}{2}\):
Using the trigonometric addition theorems
and
and after substituting the function values
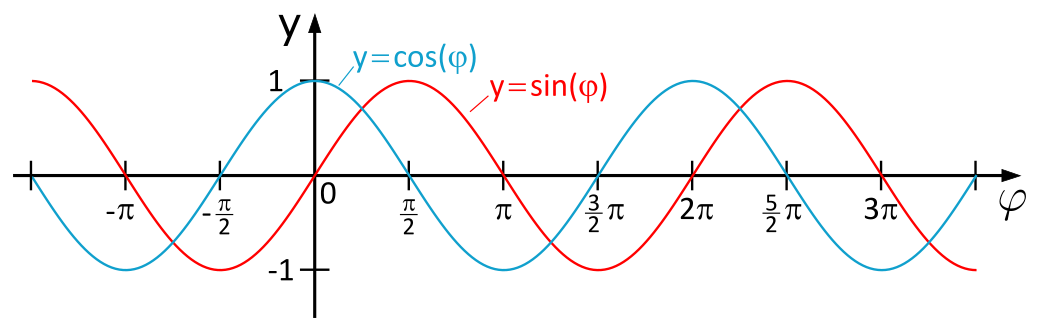
we obtain:
In summary, we have determined the stresses occurring at any angle as follows:
Using the trigonometric power formulas
and the double angle formulas
we get the transformation equations for the plane stress state:
(1.7xy)
If we know the normal stresses \(\sigma_x\) and \(\sigma_y\) as well as the shear stresses \(\tau_{xy}=\tau_{yx}\) for a perpendicular section, we can calculate the normal stresses \(\sigma_{\xi}\) and \(\sigma_{\eta}\) as well as the shear stresses \(\tau_{\xi\eta}=\tau_{\eta\xi}\) for any angle \(\varphi\) using the transformation equations.
Note:
Although there are two coordinate systems rotated to each other, the stress state for the examined point in the component remains the same. The stress state is independent of the change in the angle \(\varphi\). The numerical values of the stress state, however, depend on the angle \(\varphi\). Therefore, we only change the perspective on the stress state.
Interestingly, we can derive the equations for one-dimensional stress state (1.7xy) from equation (1.4) and (1.5xy) for the one-dimensional stress state, as in the one-dimensional stress state, \(\sigma_y = \tau_{xy}=0\):
3.1.2 Coordinate Transformation for a Cartesian Coordinate System with Positive X-Axis to the Right and Positive Z-Axis Downward
To define stresses at any arbitrary angle, we introduce a coordinate system rotated by the (cutting) angle \(\varphi\), similar to the one-dimensional stress state. We call the rotated \(x\)-axis \(\xi\) and the rotated \(z\)-axis \(\eta\).
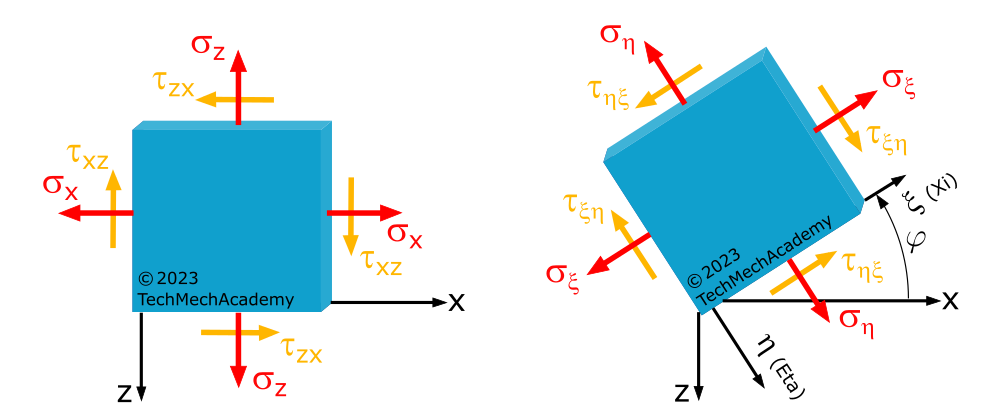
We obtain normal stresses \(\sigma_{\xi}\), \(\sigma_{\eta}\), and shear stresses \(\tau_{\xi\eta} = \tau_{\eta\xi}\).
The cutting angle \(\varphi\) is positively counted counterclockwise in the \(x, z\)-coordinate system at the analyzed element (refer to the Right-Hand Rule in the Cartesian coordinate system + Right-Hand Thumb Rule for determining the positive rotation direction).
To mathematically connect the two coordinate systems from Figure 1.3.6, we cut the area element in the \(x, z\)-coordinate system at an angle \(\varphi\) and apply stresses to the surfaces:
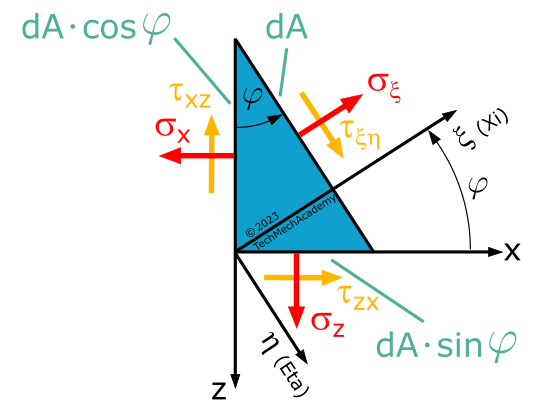
We calculate the equilibrium of forces in both the \(\xi\)- and \(\eta\)-directions.
Note:
Since equilibrium statements apply only to forces, we must multiply the stresses by the area elements on which they act!
We can factor out and eliminate \(\mathrm{d}A\) from both equations (25) and (26).
With \(\tau_{zx} = \tau_{xz}\), we then obtain:
In summary, we have determined the stresses that occur at any cutting angle as follows:
Now, we need a formula for the normal stress \(\sigma_{\eta}\). This normal stress acts at an angle of -90° (or \(-\frac{\pi}{2}\)) to the normal stress \(\sigma_{\xi}\).
So, we can use the formula for the normal stress \(\sigma_{\xi}\) we derived and replace \(\sigma_{\xi}\) with \(\sigma_{\eta}\) and \(\varphi\) with \(\varphi - \frac{\pi}{2}\):
Using the trigonometric addition theorems
and
and by substituting the function values
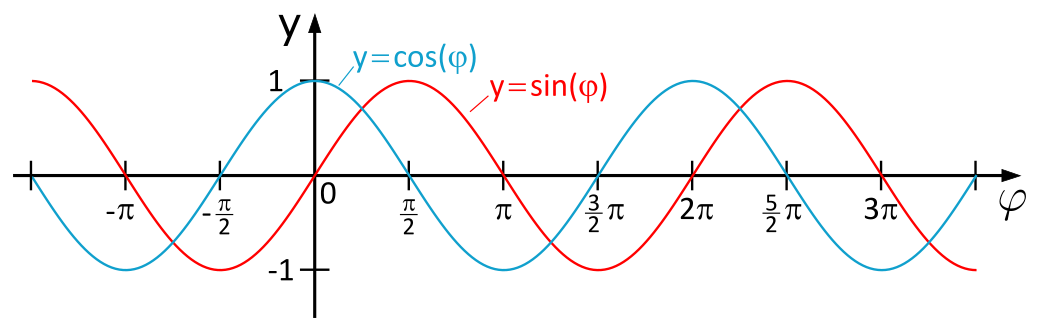
we obtain:
In summary, we have determined the stresses occurring at any cutting angle as follows:
Using the trigonometric power formulas
and the double angle formulas
we obtain the transformation equations for the plane stress state:
(1.7xz)
So, if we know the normal stresses \(\sigma_x\) and \(\sigma_z\) and the shear stresses \(\tau_{xz}=\tau_{zx}\) for a perpendicular section, we can calculate the normal stresses \(\sigma_{\xi}\) and \(\sigma_{\eta}\), as well as the shear stresses \(\tau_{\xi\eta}=\tau_{\eta\xi}\) for any angle \(\varphi\) using the transformation equations.
Note:
Although it involves two coordinate systems rotated relative to each other, the stress state remains the same for the point under investigation in the component. The stress state is independent of the change in the cutting angle \(\varphi\). However, the numerical values of the stress state depend on the angle \(\varphi\). Therefore, we are simply changing the perspective on the stress state.
Interestingly, we can derive the equations for the uniaxial stress state, as in equations (1.7xz), as from equation (1.4) and (1.5xz) for the uniaxial stress state, because in the uniaxial stress state, \(\sigma_z = \tau_{xz}=0\):
3.1.3 Sum of Normal Stresses at Any Cutting Angle
By adding the first two equations from (1.7xy) or (1.7xz), we gain the insight that the sum of normal stresses for a point within a plane in the component remains constant at any cutting angle \(\varphi\):
(1.8)
FAQ: How to Open a Link in a New Tab?
There are 3 Ways to open a link in a new tab:
-
Method 1: Ctrl+Click
The first method requires a keyboard and a mouse or trackpad. Simply press and hold the Ctrl key (Cmd on a Mac) and then click the link in your browser. The link will open in a new tab in the background.
Note: If a link points to content on the same page, it is not possible to display that content in a new tab using this method.
-
Method 2: Mouse Scroll Wheel
If you use a mouse with a scroll wheel, you have one of the easiest ways to open links in new tabs. Simply put the cursor over the link and click the scroll wheel. The link will open in a new tab in the background.
-
Method 3: Right-Click Menu
The last method is probably the one most people know. but it's not as quick as the other methods. When you see a link you want to open in a new tab, right-click it. You can then select "Open Link in New Tab" from the menu.